Dyson Automotive update 10th October 2019
"The Dyson Automotive team have developed a fantastic car; they have been ingenious in their approach while remaining faithful to our philosophies. However, though we have tried very hard throughout the development process, we simply cannot make it commercially viable. We have been through a serious process to find a buyer for the project which has, unfortunately, been unsuccessful so far. I wanted you to hear directly from me that the Dyson Board has therefore taken the very difficult decision to propose the closure of our automotive project.
This is not a product failure, or a failure of the team, for whom this news will be hard to hear and digest. Their achievements have been immense – given the enormity and complexity of the project. We are working to quickly find alternative roles within Dyson for as many of the team as possible and we have sufficient vacancies to absorb most of the people into our Home business. For those who cannot, or do not wish to, find alternative roles, we will support them fairly and with the respect deserved. This is a challenging time for our colleagues and I appreciate your understanding and sensitivity as we consult with those who are affected.
Dyson will continue its £2.5bn investment program into new technology and grow our wonderful new University. We will continue to expand at Malmesbury, Hullavington, Singapore and other global locations. We will also concentrate on the formidable task of manufacturing solid state batteries and other fundamental technologies which we have identified: sensing technologies, vision systems, robotics, machine learning, and AI offer us significant opportunities which we must grab with both hands. Our battery will benefit Dyson in a profound way and take us in exciting new directions. In summary, our investment appetite is undiminished and we will continue to deepen our roots in both the UK and Singapore.
Since day one we have taken risks and dared to challenge the status quo with new products and technologies. Such an approach drives progress, but has never been an easy journey – the route to success is never linear. This is not the first project which has changed direction and it will not be the last. I remain as excited about the future of Dyson as I have always been; our ambitions have never been higher, our ability to invest has never been greater, and the team has never been stronger.
I am looking forward to our future adventures together."

James Dyson
Engineer
The Dyson Battery Electric Vehicle
By James Dyson

An obsession with solving problems
Dyson's first foray into the automotive world came in 1990, when we began work on a cyclonic filter that could be fitted onto a vehicle's exhaust system to trap particulates. In 1993, James Dyson went on British national television to explain how this technology worked.
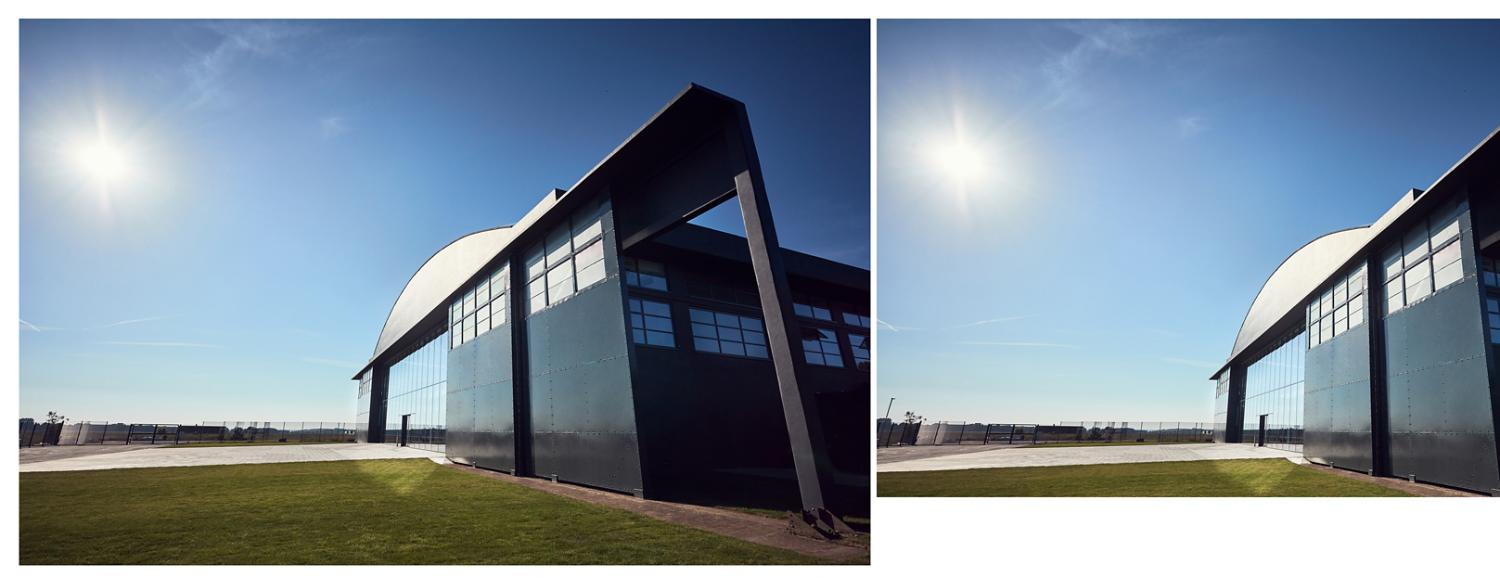
Engineering the future
Dyson continues to invest in the UK and Singapore across Research, Development and Commercial operations. The 517 acre Hullavington technology campus in the UK will be a backdrop to exciting future developments and we will outline those plans in due course.
Rich in aeronautical history
-
Celebrating aviation
Once decaying, the Hullavington campus has been meticulously restored to celebrate its aviation history. It’s also the completion of a journey for building contractors Kier, who are redeveloping the site they first built more than 80 years ago – to start a new journey for Dyson.
-
Home to the Whittle gas-turbine engine
One of the many components stowed here from 1939 was the iconic Whittle gas-turbine engine, which helped change the very nature of aviation. Just as the engine was used to teach aircrew, today a restored Whittle engine is regularly powered up to inspire Dyson engineers at our Malmesbury campus.
-
A teaching airfield
Formerly a Ministry of Defence airfield, this vast site was built in 1937 primarily for training aircrew and flight instructors, as well as a base for 1,000 aircraft.
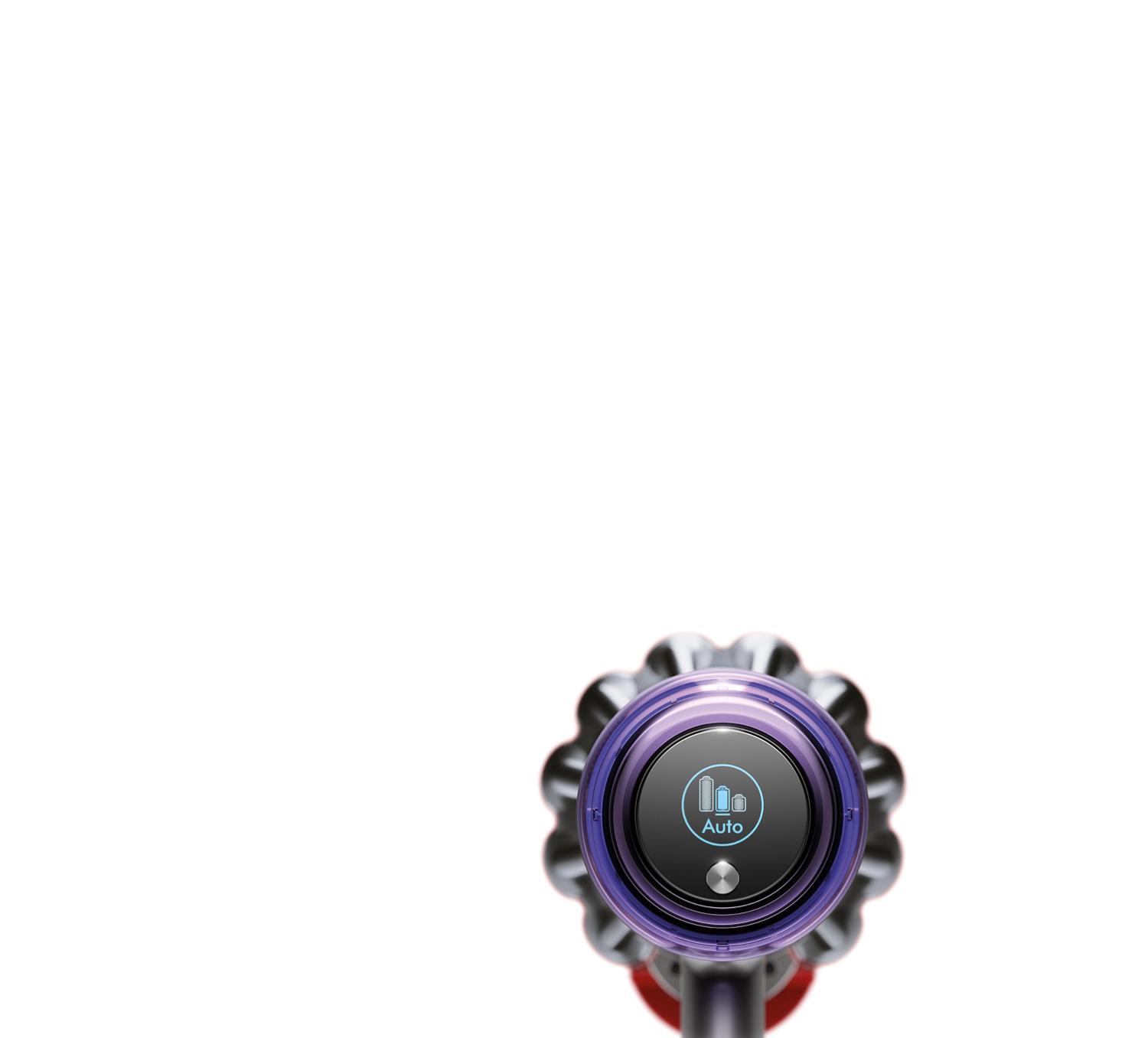
Explore Dyson engineering